6.6.4 Retaining Cylindrical Metal Assemblies
Retaining compounds are used in circumferential assemblies with one part inserted into the other. A typical example is a bearing mounted in an electric motor housing.
Retaining compounds achieve maximum load transmission capability with reduced interference, uniform stress distribution and no fretting corrosion. Applied as a liquid, they form a 100% contact between mating metal surfaces, eliminating the need for expensive replacement parts, time-consuming machining or the use of mechanical methods.
The major advantage of adhesives is that they require less machining tolerance and no securing parts. Following the same anaerobic curing principle, the retaining compound adhesives fill the gap between the matching parts, creating a unitised assembly and simplifying the design, production, assembly and repair of parts.
Retaining compound adhesives have excellent resistance to rotational force and can be disassembled by applying shear force.
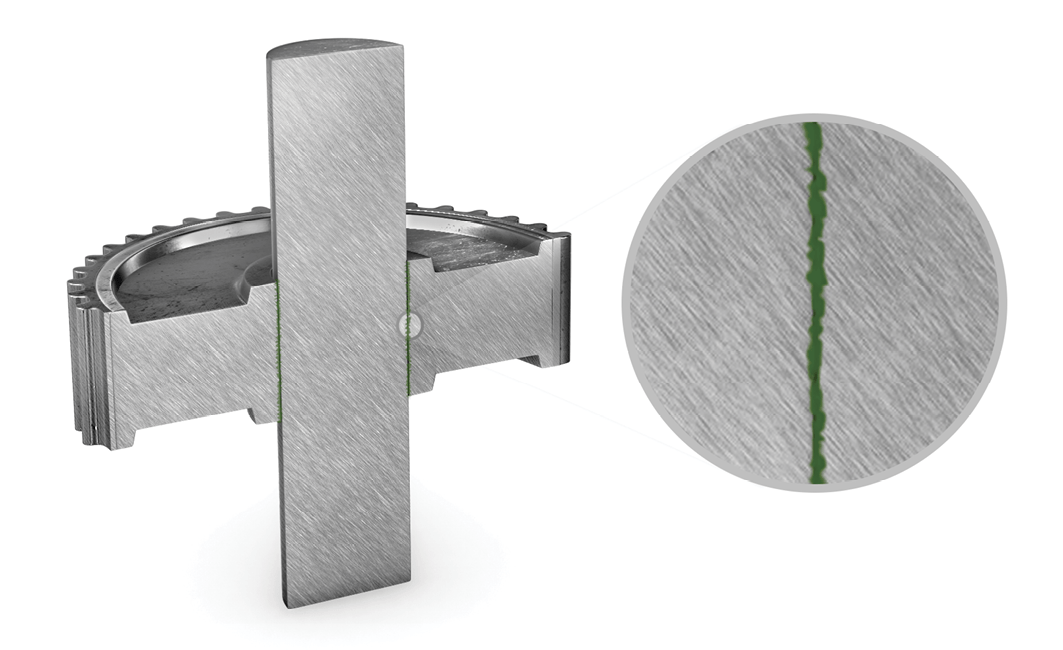
Advantages of retaining compounds
- Provide a significant increase in strength with existing geometries
- Allow lower interference achieving similar strength levels
- Lead to lower stress levels in the hub
- Enable smaller and lighter part geometries
- Allow the use of light-weight materials
- Seal the joint and eliminate corrosion