5.2.1.11 Calculating Strength in Bonded Assemblies
No matter the application, industry, material or adhesive, engineers and technicians are always asking a simple question: How will we know an adhesive is strong enough? In a world where many mechanical assembly methods are being replaced with chemical adhesive bonding, ensuring the strength, safety and reliability of a finished assembly is of the utmost importance. There are as many ways of testing strength as there are assembled parts, ranging from pull-out strength tests on bonded medical needles to head-on crash testing of automobiles in windscreen bonding applications. Different failure modes can also be tested. For example, peel strength may be more important than tensile or shear strength in a highly flexible assembly. Another example is that impact resistance might be the most important factor for a structural adhesive used to bond body panels on a vehicle.
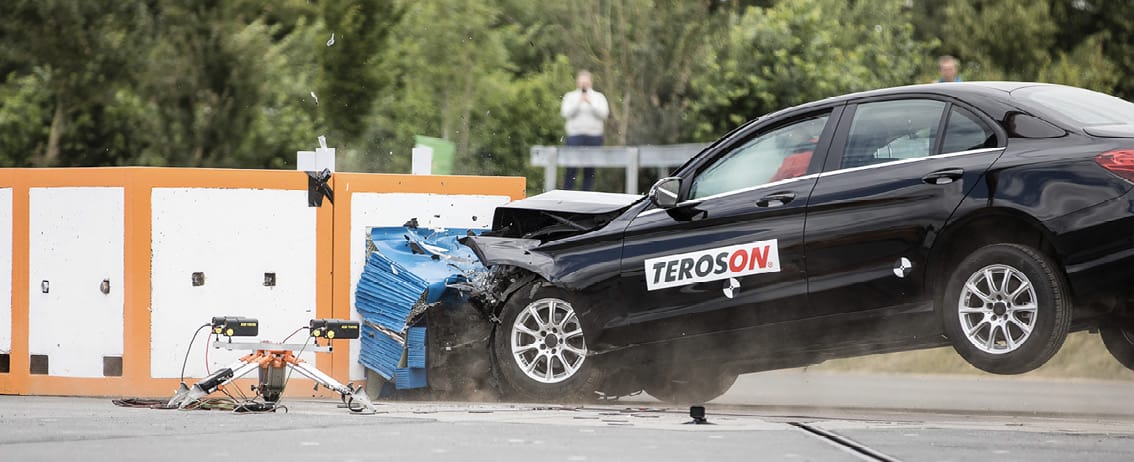
It is ultimately up to design and production engineers to determine a test metric that best correlates to the real-world performance of their product, and thankfully there are many industry test methods and standards to help guide that process. These test methods are usually performed during both the design process (adhesive qualification testing) and production (quality control tests). Quality control engineers and technicians must be careful not to test products before the adhesive has had sufficient time to cure, lest the results of that test misrepresent the performance of the adhesive and the assembly. While simulated testing is the most accurate way to assess the strength of bonded assemblies, there are some methods for approximating bond strength.
Calculating estimated bond strength goes back to one of the most basic principles of adhesives: stress distribution. Traditional assembly methods, including rivets, nuts and bolts, spotwelds and clamps, tend to concentrate the load-bearing interface of the parts in a very small surface area, leading to stress points which are usually the points of failure for an assembly (see Section 4). Alternatively, using adhesives distributes the load over a larger surface area, allowing the assembly to withstand greater loads.
The larger the surface area, the lower the stress. Consider the following equation for the shear stress of a joint, where σ is the stress, A is the surface area of the bond and F is the force of an external load.
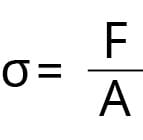
Assuming that the stress is equal over the entire surface area, there is a proportional relationship between the force and the stress in the bond line and an inversely proportional relationship between stress and surface area. Since failure occurs when σ exceeds the yield stress of the bond itself, engineers should design assemblies to minimise this stress. Therefore, either the applied force must be minimised, the surface area must be maximised, or both. In most applications, controlling the forces or external conditions experienced by an assembly is not possible. For example, engineers cannot control stress in the automotive windscreen bond line when collisions occur. However, engineers can design the interface of the windscreen and the car body panels to maximise surface area. Therefore, a maximised surface area is directly related to maximised adhesive performance.
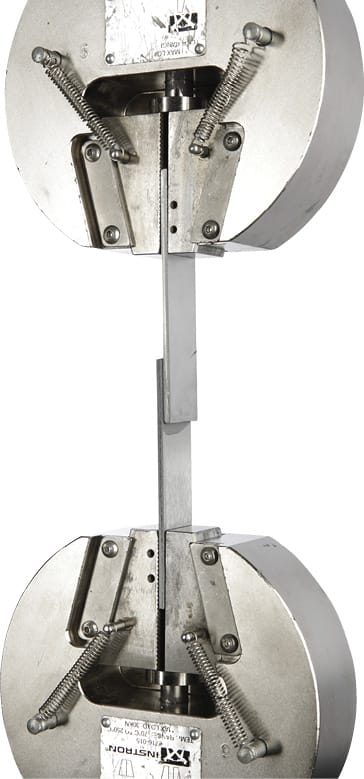
The information available on the TDS will vary depending on the product. However, the most common test result included will be shear strength, which also happens to be one of the most popular methods for evaluating adhesive performance, following ISO 4587.14 While shear strength is usually a good indicator of how well an adhesive will bond to the surface of a material, it may not necessarily be an indicator of performance. For this reason, engineers should pay close attention to the differences in the predicted (calculated based on surface area) and observed strength.
In fact, many factors can cause differences in the observed strength results versus the calculated results. Thinking about surface cleanliness, the top surface may be contaminated or simply covered in a protective coating such as a powder coat or paint system. Furthermore, even the same material listed on the TDS may have different adhesion depending on the grade, alloy, blend or even manufacturing batch. For these reasons, rough calculations based on technical data may be a good starting point for selecting an adhesive, but the best practice is to always perform testing to verify the level of performance in the conditions that are most relevant to the integrity of the assembly. Later sections will provide more insights into how observed testing results may be interpreted.
14) International Organization for Standardization, ‘ISO 4587 Adhesives - Determination of Tensile Lap-Shear Strength of High Strength Adhesive Bonds,‘ 2003.