5.1.7 Joints with Thin Substrates
In general, thin substrates are bonded using simple overlapping joints or slightly modified joints. The double strap configuration is one of the most effective for this application.
For thin materials, two important considerations should be noted:
- The material used for reinforcement, or straps, must be made of the same or similar material with equivalent strength, flexibility and thickness as the assembly substrate.
- The adhesive should have the same degree of flexibility as the substrates or greater flexibility than the substrates.
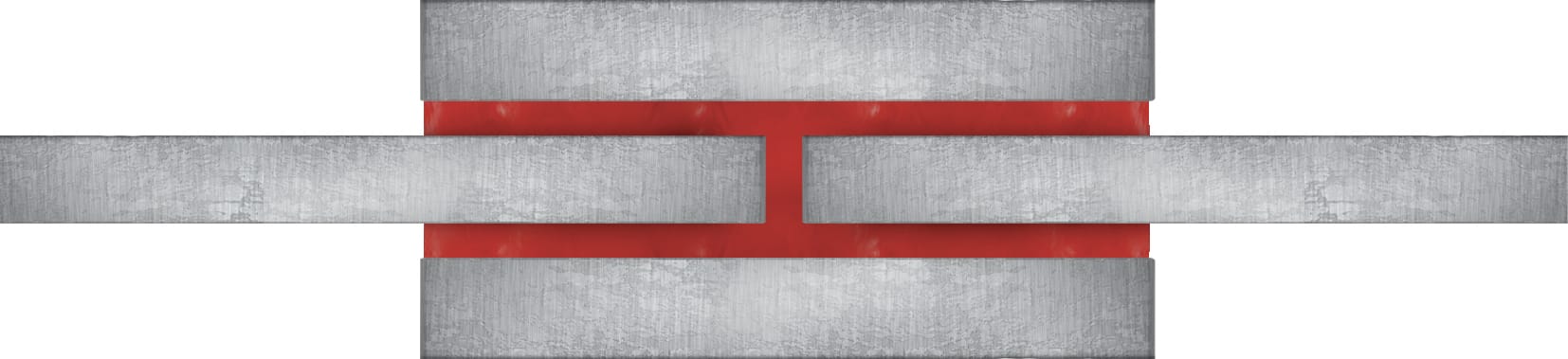
The thickness of the substrate is a very important variable for consideration. As the substrate thickness varies, so does the distribution of stresses within the joint and assembly; therefore, reinforcements to the joint may be required. As the thickness of the substrate decreases, the assembly will be more prone to peel forces. Conversely, as the thickness of the substrate increases, the assembly will be less prone to peeling forces.
If the substrate(s) depth is large enough, configurations with a scarf joint can be used; the appropriate thickness, where this becomes practical, will vary by substrate type. Ideally, the joint length (L) should be four times the size of the thickness (t) or greater.
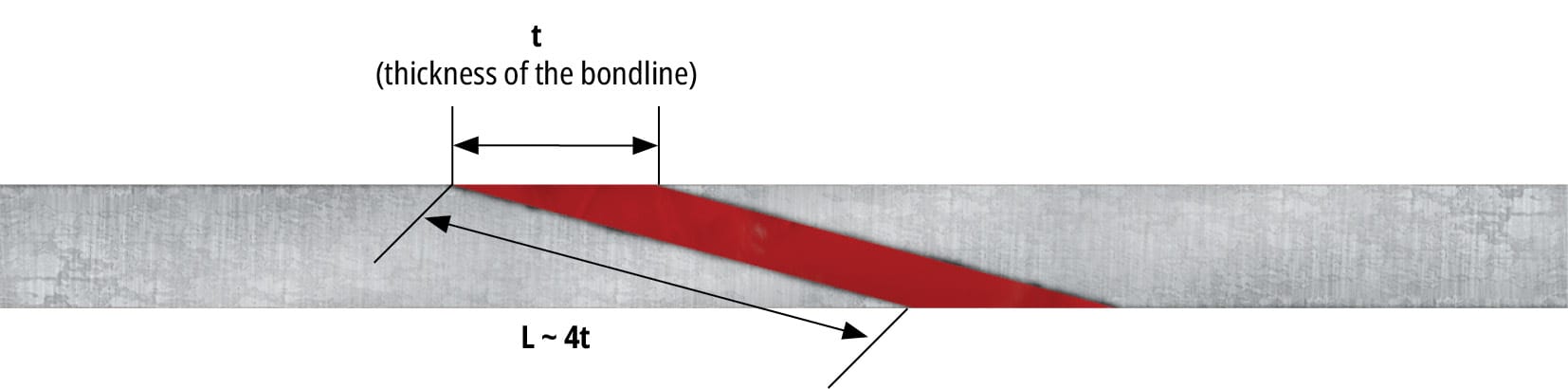
Plastic matrix composites have physical and mechanical properties that depend on the direction in which the joint is made; this is referred to as anisotropy. The component should be designed so that the substrate is stressed in the preferred direction.
To avoid peeling forces when bonding thin or flexible substrates to metal:
- Avoid geometries with very acute angles to reduce excessive stress concentration.
- Increase the stiffness of the metal substrate to limit the occurrence of peel phenomena.
Adopt joint geometries that favour the stressing of the adhesive in its preferred direction (avoids peel).
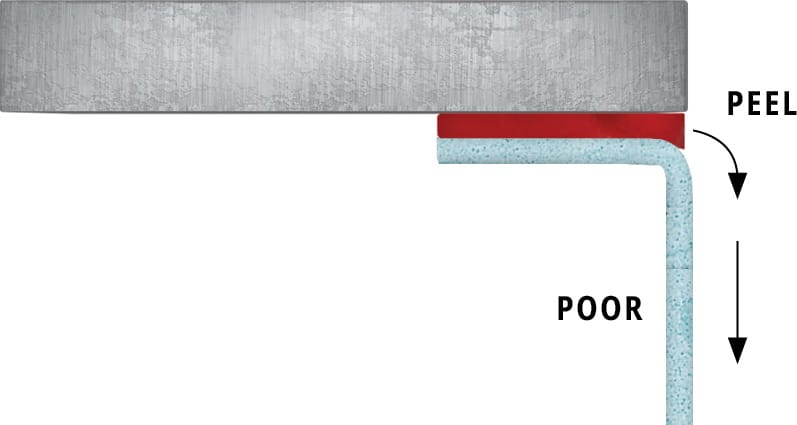
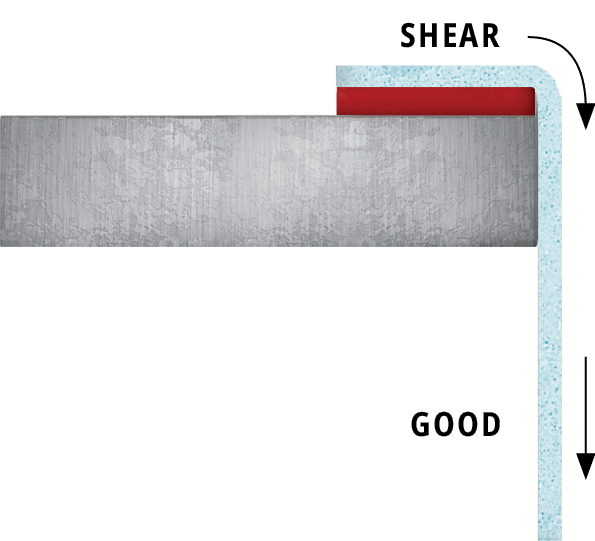
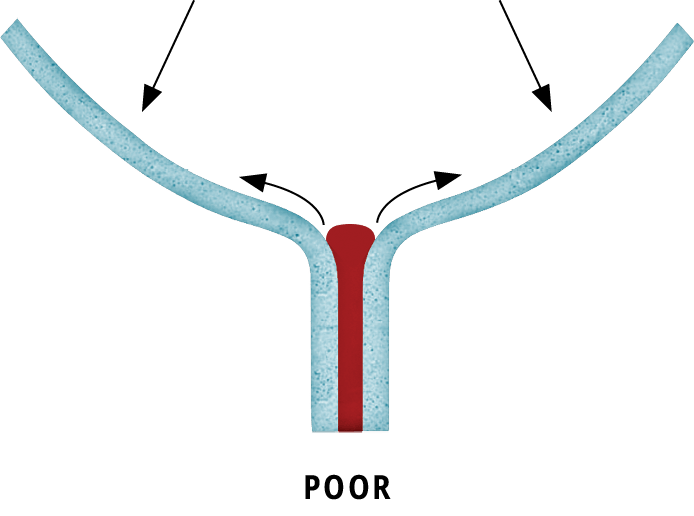
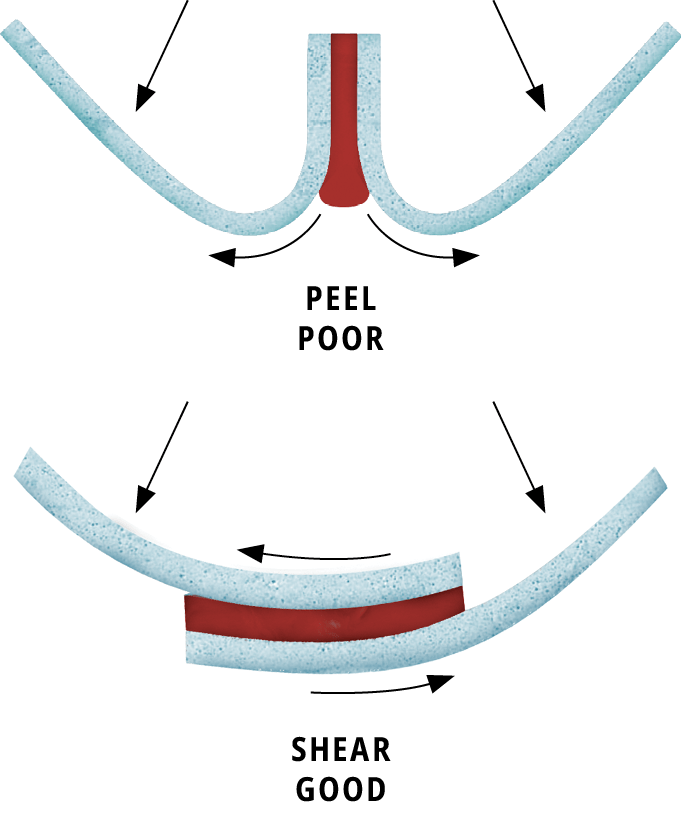
The final consideration is that it is important to limit the stresses on the substrate during the adhesive curing phase, as excessive clamping pressure may lead to residual stress at the interface.