4.4.7 Fatigue stress
Fatigue stress is repetitive cyclic loading. The vibration from traffic on a bridge, persistent force on a wind turbine, keystrokes on a keyboard and automotive shock absorbers are all examples of fatigue stress. Like impact, fatigue is a dynamic form of stress.
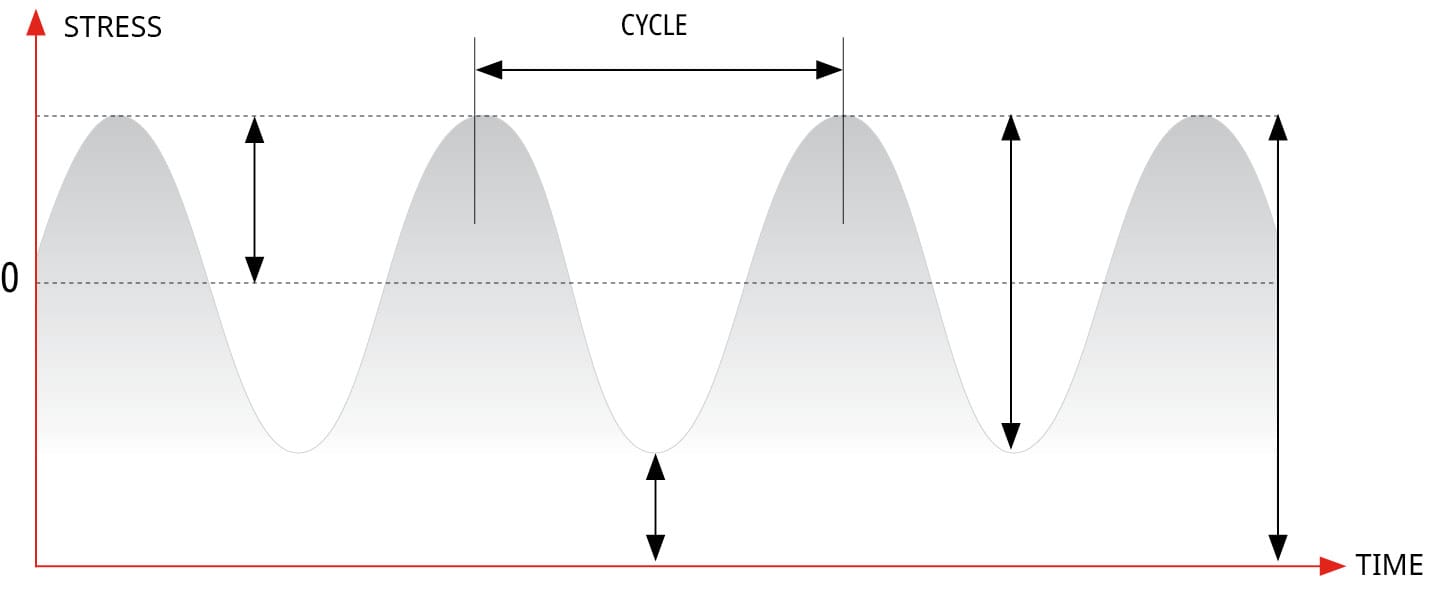
A material or assembly that will withstand a large static load may fail at a much lower load if it is cyclic and repetitive. Fatigue testing seeks to predict the working life of an assembly by testing specimens under cyclic loading at multiple stress levels. Life cycle predictions based on these results may be used to schedule the replacement of these parts before the anticipated failure.
Fatigue parameters include amplitude, frequency and wave shape. Polymers (adhesives included) are normally tested below a frequency of 60 Hz to avoid heating the material, which would introduce an unwanted condition into the test. One hundred percent strength is determined by testing the specimen to failure in a static test; fatigue cycling is then performed at ever-decreasing levels until a level is reached that will endure ‘indefinitely’, or 107 cycles, as a practical rule-of-thumb. An S-N graph is plotted with stress on the y-axis and the number of cycles on the x-axis. A best-fit line that appears asymptotic indicates that the assembly may survive indefinitely at this stress level: ISO 9664 defines this as the fatigue limit. If the plot continues to slope downward at 107 cycles, this is reported as the endurance limit at 107 cycles. Note: ASTM uses slightly different terminology; the identification of test results must reference the source test for clarity.
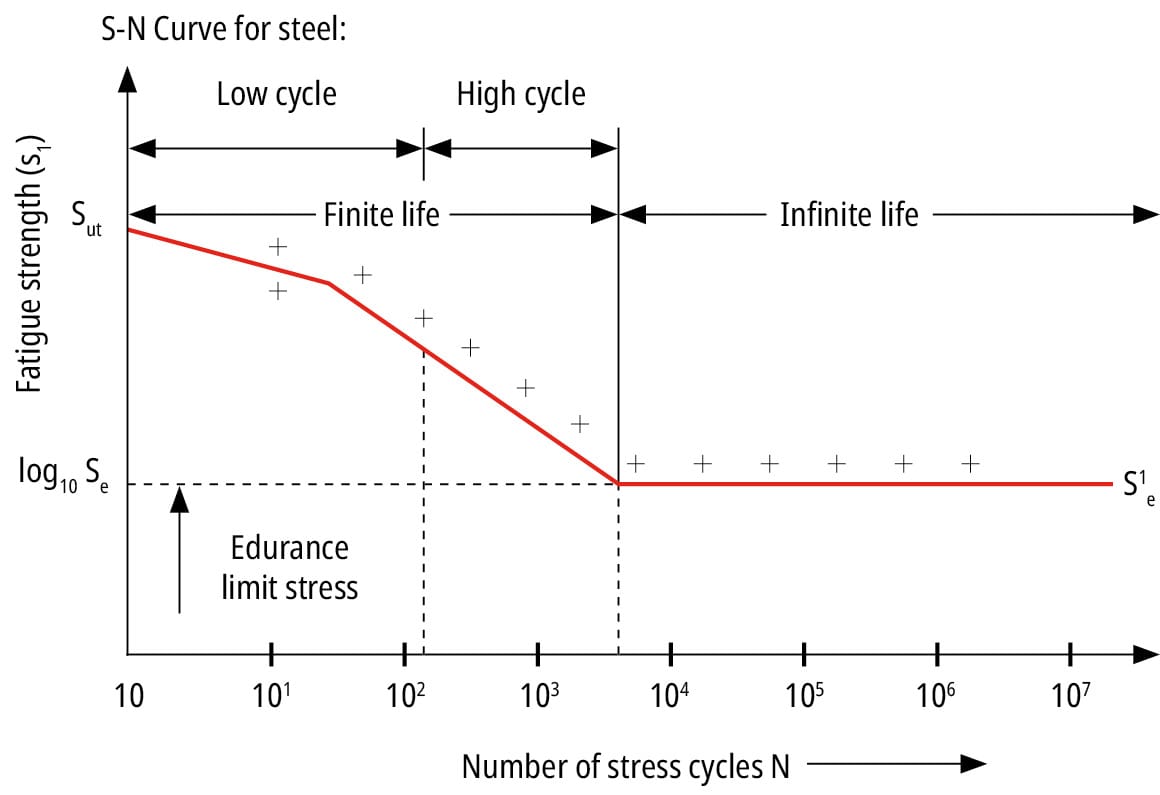