4.3.3 Surface Preparation: Mechanical Abrasion and Roughening
Increased bond strength is a beneficial side effect of cleaning by mechanical abrasion. Substrate surfaces are frequently roughened to take advantage of this, regardless of any cleaning requirements.
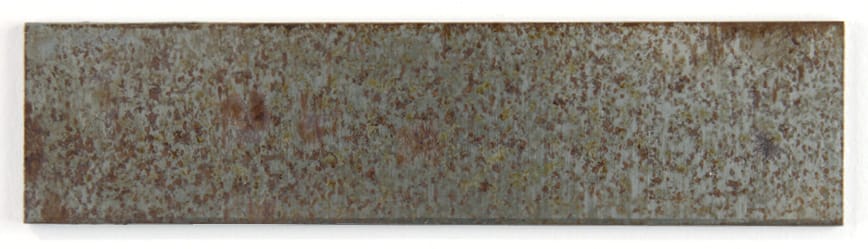
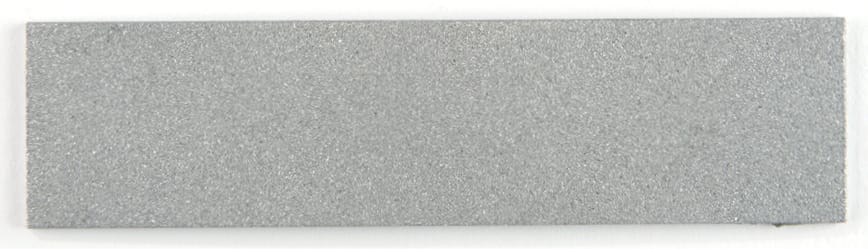
Roughening a surface increases bond strength in two ways. The roughened surface presents a larger bond area and adhesive, which flows into microscopic cracks and porosity of the surface, cures solid and mechanically locks into the surface.
The beneficial effect of roughening substrates is measurable, as shown in Table 14.
Adherend Surface Treatment | Tensile Strength N/mm2 (psi) | Strength Difference from Polished Surface Finish |
Polished, 1 µ diamond dust | 28.8 ± 7.0 (4,180 ± 1,020) | n/a |
Abraded Through 600 paper | 30.9 ± 7.7 (4,480 ± 1,120) | + 7.2% |
Abraded Through 280 paper | 39.0 ± 6.8 (5,660 ± 0,990) | + 35.4% |
Abraded Through 180 paper | 36.7 ± 7.5 (5,320 ± 1,090) | + 27.3% |
Sandblasted (40-50 grit) | 48.5 ± 7.0 (7,030 ± 1,020) | + 68.2% |
Profilometer and scanning electron microscope (SEM) analyses show differences in surface profiles after mechanical abrasion.
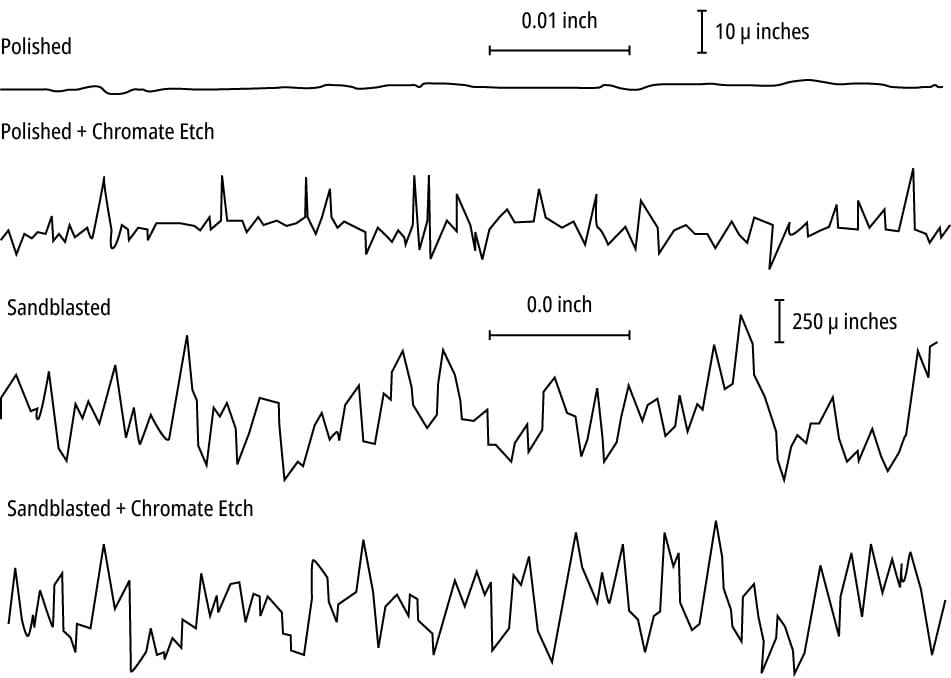
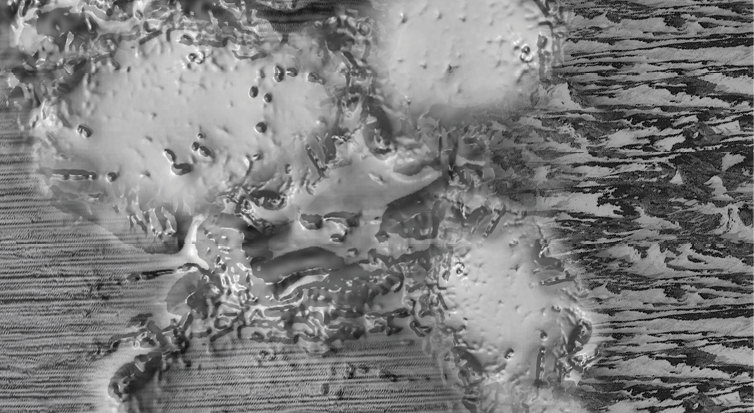
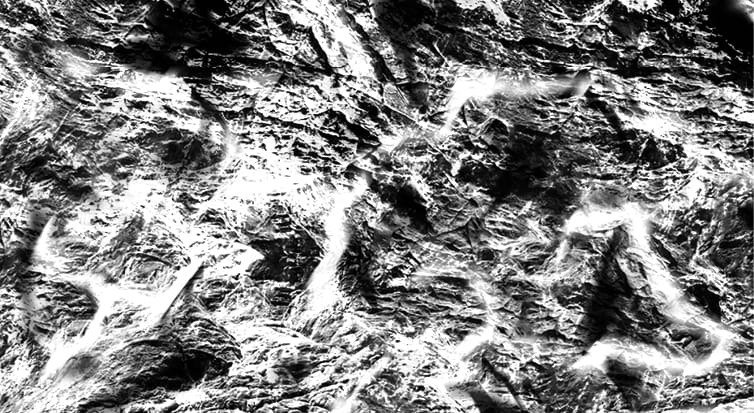
Some caveats exist for the mechanical abrasion of substrates: extreme roughness and large pores require more adhesive to fill and may take longer to cure. Adhesives that perform best in thin layers may be less effective on highly textured surfaces – check with the adhesive’s manufacturer for recommended surface finishes. The cohesive strength of the adhesive layer (its internal strength) will not be increased by roughening the substrate, so assemblies suffering cohesive failure will not benefit from surface preparation.
For applications that benefit from roughening the substrate, a preferred range of surface roughness can be found experimentally. The following graph demonstrates the shear strength of an adhesive with increasing surface roughness on both steel and aluminium substrates.
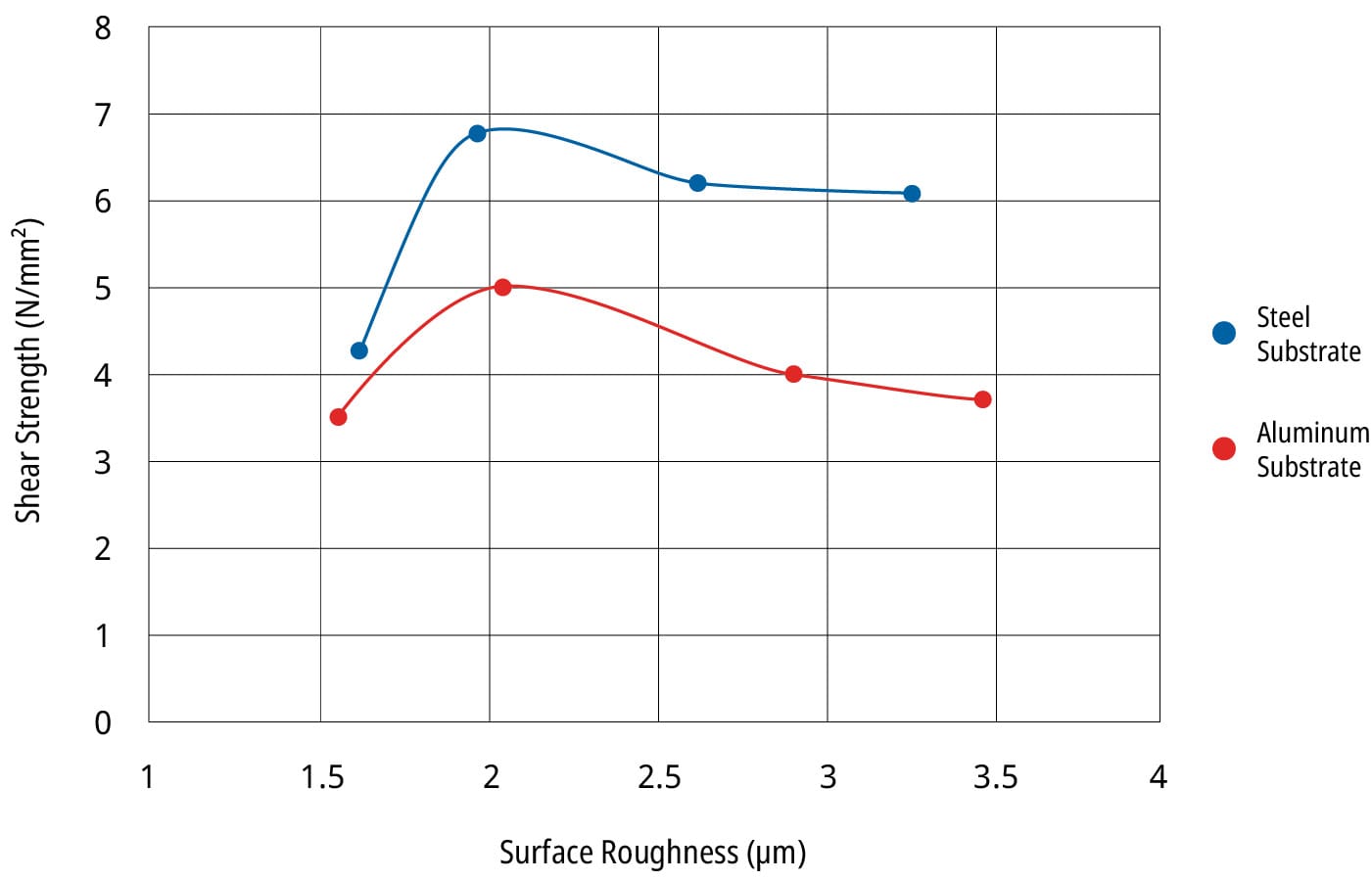