4.3.2.3 Abrasive Blasting
Abrasive blasting cleans by shooting corundum, aluminium oxide, silicon carbide or other abrasive blasting media at a surface. Systems can work by injector, using the vacuum of a venturi nozzle to draw abrasive particles from a reservoir and shoot them at the surface or by pushing both air and abrasives from the same pressurised reservoir. Blasting systems emit dust, so they are best used in closed, covered and well-ventilated areas. These systems require trained operators and health and safety precautions for use. Figure 87 shows one of the most common surface preparation methods: grit blasting.
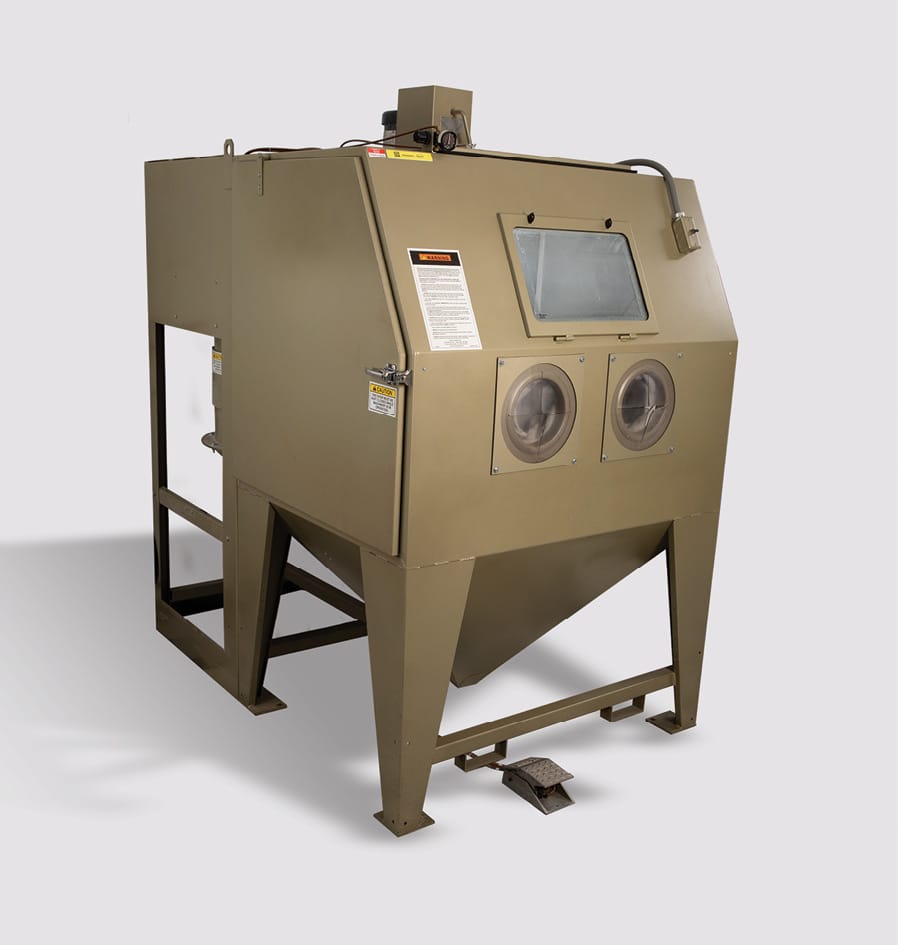
4.3.2.4 Dry Ice Blasting
Similar in operation to injector-type abrasive blasting systems, dry ice blasting systems fire CO2 pellets at temperatures of -78.5°C (-109.3°F) onto a part’s surface. The pellets initiate a thermal and mechanical cleaning process by freezing the surface contaminants while the substrate remains at an ambient temperature. As the CO2 pellets sublimate, they increase in volume, thereby dislodging the contaminants. This method is effective for cured adhesives, paint and other contaminants without mechanical abrasion. There is no gritty residue, no additional chemicals and less machine maintenance than traditional blasting cabinets.