4.3 Surface Preparation for Adhesive Bonding
Surface preparation prepares the substrate for the best possible bond. Proper surface preparation goes beyond just cleaning the substrates and includes various methods to improve an adhesive’s grip on the surface of the substrate. The surface energy of plastics may be increased via plasma, corona or flame treatments for better wetting on the surface and therefore a stronger bond. An increase in surface roughness by abrasion or other methods is a proven way to increase bond strength by increasing the surface area. Chemical means of surface preparation include primers and adhesion promoters for bonding to difficult-to-bond surfaces.
4.3.1 Cleaning
Any barriers to surface contact will reduce an adhesive’s bond strength. Such barriers include accidental contaminants like dirt, rust and oil or intentionally applied materials like detergents or protective films. Metal may be contaminated with cutting oil or corrosion inhibitors. Injection-moulded plastics typically have mould release on their surfaces. Table 9 shows some common sources of contamination.
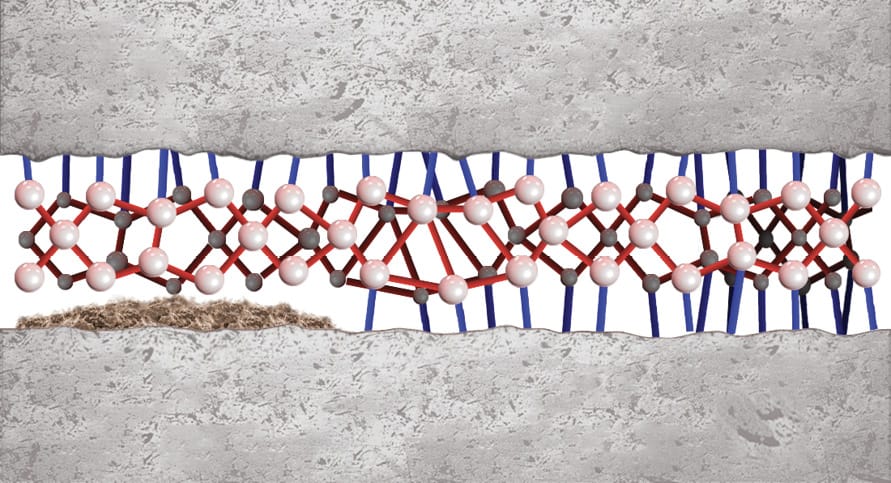
Source of Contamination | Contamination |
Manufacturing processes | Release agents, graphite content in cast iron, drawing lubricants |
Handling | Oils |
Environment | Moisture, dirt and dust |
Machining processes | Cutting fluids, swarf, corrosion inhibitors |
Inactive layers | Oxide layers (metals) protective oil, e.g. black oxide steel bolts |
Residues from galvanic processes | Metallic protective coatings like zinc, nickle, phosphate or chromate |
Cleaning processes | Residues from alkaline baths or industrial cleaners, corrosion inhibitors |
One cleaning step to remove all contaminants is preferable. However, depending on the nature of the contamination on a substrate, multiple methods may be required. Multiple forms of contamination are typically present, especially on used parts. In addition to removing contaminants, the cleaner used must be compatible with the substrate and the adhesive. Cleaners must also follow health, safety and environmental standards, such as those for volatile organic compounds (VOC) and biodegradability. The drying time of a cleaner and the required equipment must also be considered in the choice of cleaners. Table 10 outlines considerations when choosing a cleaning process.
Application Detail to Consider | Importance of Consideration |
Type of Contamination | The cleaner should be selected based on the chemistry of the contamination; polar/nonpolar, inorganic/organic. |
Process | Equipment: dip tank, spray, wipe, etc. Time: solvent evaporation, secondary residue removal |
Parts being cleaned | Compatibility – does not chemically attack the substrate |
Adhesive system | Compatibility – does not affect cure mechanism; no residue to act as a release agent |
Health and Safety of Operators | Cleaners should comply with health and safety standards to protect workers and the environment. |
Multistep cleaning should follow a particular order. While new parts may only need solvent or aqueous cleaning to be ready for bonding, parts with loose particulate, rust, old paint or old adhesive will require multiple cleaning steps. Before abrasion with sandpaper, wire wheel, grit blasting or other aggressive, mechanical abrasion, the surface should be cleaned with a solvent or aqueous cleaner to prevent contamination from being driven further into the surface. After mechanical cleaning or abrasion, a solvent will remove loose debris and lingering contaminants. Aqueous cleaners should not be used on freshly mechanically cleaned or abraded metal parts due to the risk of flash rust. This sequence also applies to mechanical abrasion intended to increase bond strength by roughening.
Once cleaned, parts should be bonded immediately or stored where they are protected from recontamination. Metals prone to oxidation should be bonded or treated with a rust preventative shortly after being cleaned.
The following cleaning methods may be used alone or in combination, depending on the needs of each part.