3.1.8 Recreational Vehicles
Recreational vehicles, including trailer caravans, should be robust and lightweight. Adhesives are used to produce the laminated (sandwich) elements for the caravan construction. Historically, the standard method for joining the laminate elements was to fasten them together mechanically and seal the joints with a non-curing sealant. Some recreational vehicle manufacturers have eliminated up to 90% of the screws used in their vehicles by using adhesives.
Henkel partnered with Elddis, a UK-based RV (caravans, motorhomes and van conversion) manufacturer, to prove this adhesive concept. A caravan was manufactured using the existing design, and the screws were replaced with a structural polyurethane (PU) adhesive and an elastic-modified silane adhesive, as appropriate. This bonded caravan was then heavily tested without breaking or showing signs of fatigue. The joint design was then optimised for use with adhesives for both strength and water tightness. This new design increased the bond area of the frame by 63%, making the structure lighter and ten times stronger than the precursor.
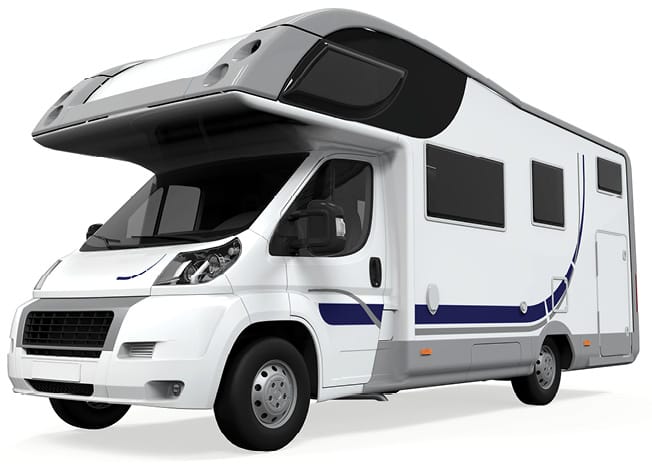
Using adhesives instead of mechanical fasteners reduces the need for stiffeners and offers the freedom to choose and combine a broad range of materials to create new designs. Liquid ingress is a recurring issue in the recreational vehicle industry; eliminating approximately 800 screws eliminates as many potential leak paths as possible, thus reducing warranty claims. In this example, it allowed the vehicle manufacturer to double the bodyshell warranty time for the bonded construction compared to the original design which used screws and mechanical fasteners.