3.1.5 Prominent Industries and Applications
The transportation sector includes industries that have benefited from the advantages that adhesives offer for the longest time. When the first adhesive factories opened in Europe around 1700, it was quickly found that bonding materials could be beneficial in transportation applications. There were drawbacks to the adhesives made at this time, which were animal-based. These adhesives were not resistant to heat and water, making them only usable in areas on vehicles, such as wagons, carriages and trains, that were not exposed to hot and wet conditions.
In 1911, when automobiles and carriages shared the streets, Carriage Monthly magazine wrote about a new ‘waterproof glue’. When combined with formaldehyde, this animal-based glue could be applied cold and survive in wet environments. General-use automotive bonding adhesives were finally possible because of this innovation.11
11) ‘Carriage Bodies and Parts,’ The Carriage Monthly, April 1911, p. 20.
3.1.6 Automotive Industry
The automotive industry is a significant driver in using adhesive technology. Many adhesive technologies are used in both the production and repair of modern vehicles. Adhesives make it possible to combine all types of diverse materials with strength, stiffness, corrosion resistance and, in many cases, a simpler manufacturing process. The windscreen of a vehicle is bonded in place instead of being squeezed into a rubber profile, as it was before. This not only offers sealing capabilities but also adds stiffness to the car body. Thinner and lighter glass can be used, thus decreasing the overall weight of the vehicle. Using adhesives to bond the windscreen increases safety by keeping passengers inside the car, acting as a backboard for the airbags and preventing the roof from being crushed in a crash scenario.
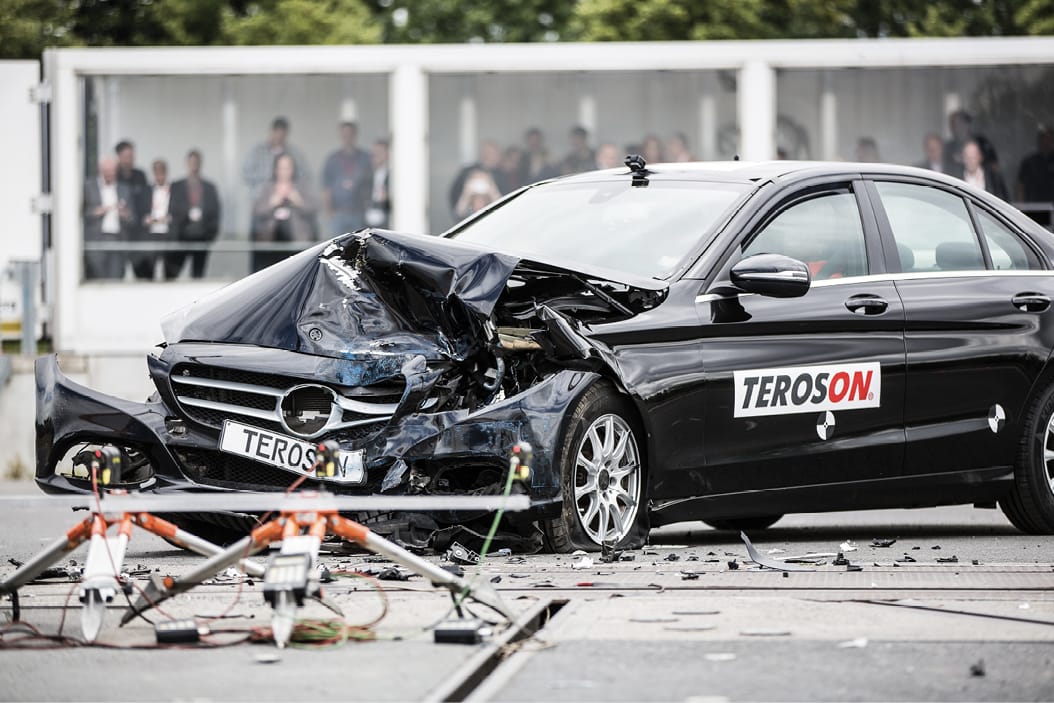
The successful use of bonding windscreens led to the use of adhesives in the body structure to add stiffness, reduce welds and provide sealed seams for extra corrosion protection and to prevent fluids entering the interior of the car (moisture, rain and exhaust gases). Bonded constructions offer more even energy absorption in the case of a crash than a spot-welded construction. Adhesives are used to reinforce pillars, as shown in Figure 68. The adhesives add stiffness without using a thicker metal, thus reducing the overall weight of the vehicle.
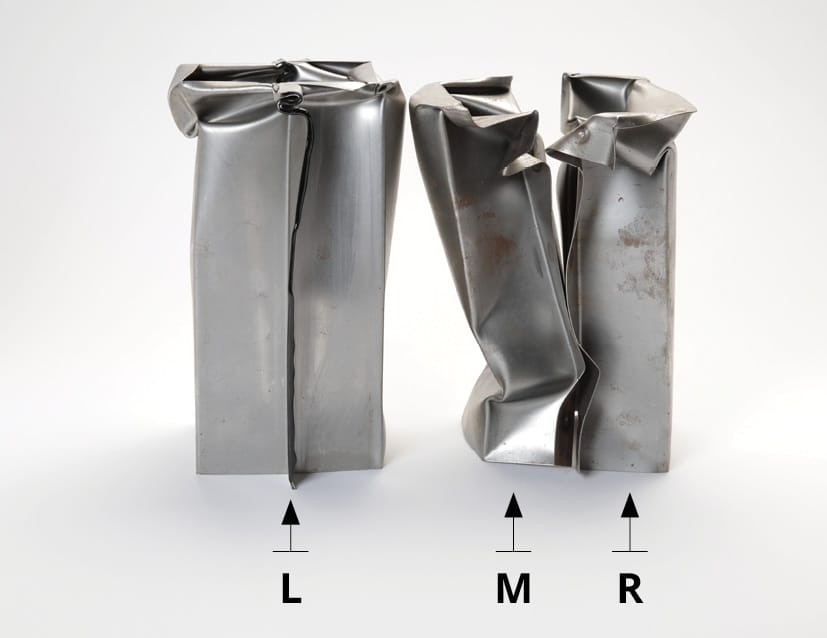
Other exterior applications for adhesives include roofs made of different materials, such as metals, glass or fibre-reinforced plastics bonded in place, mirrors, lamps, bumpers, spoilers and door flanges. Inside the vehicle, adhesives are ideal for laminating and bonding all interior components, including door panels, displays, dashboards, headliners, cockpit and instrument panels, and seat trims.
The powertrain of a car also contains many adhesive applications for sealing against different liquids and bonding within the engine, transmission, differential and driveshaft. For example, anaerobic retaining compounds are used to replace or improve traditional splines, press and shrink fits; they add strength, improve reliability and reduce the risk of fretting, contact corrosion and rust. Retaining compounds will also reduce the costly machining required to achieve complicated designs and narrow tolerances required for traditional methods. In hybrid and electric vehicles, the propulsion system includes the battery, electric drive system and control electronics. Adhesives are commonly used for sealing, encapsulation and heat transfer in these systems.
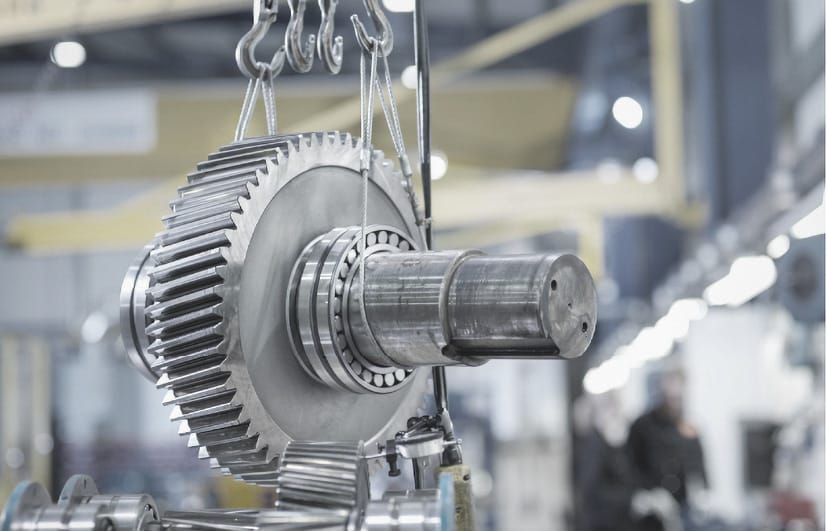
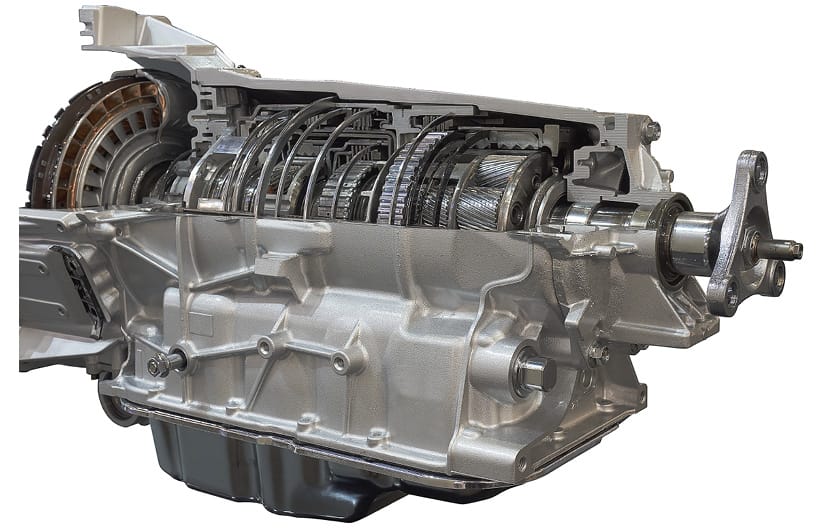