2.2.4.4 Impact and Shock
Figure 54 Impact
Impact and shock are externally acting forces that designers often account for, but knowing the location, direction and magnitude of the impact is nearly impossible to predict. Many industries, notably the automotive, aerospace and rail industries, conduct extensive modelling and failure modes and effects analysis (FMEA) calculations. In applications where there is a greater risk to life in the event of an impact or crash, these analyses and tests ensure that the performance of a product or vehicle is fit for its purpose and is safe. Often, it is not how resistant to shock or impact a material is that will allow its selection and inclusion within a design, but how it will transfer the load through itself and deform with or against surrounding materials or components. Plastic and aluminium body panels are selected for their lightweight and processing properties but also for their ability to deform during a crash and transfer the shock loading through various planes to surrounding, stronger components, such as vehicle crumple zones. It is the behaviour of a material under such conditions that may lead to its selection. The same is true for the method of joining parts and securing them together. A riveted assembly has numerous localised stresses within the materials due to the joining method and process. Usually, parts are torn along such seams when great shock and impact loads are applied. A clipped assembly may perform similarly, where the clip fasteners also deform due to impact and allow the previously joined substrates to move away from each other freely. This results in an uncontrollable deforming of parts that may not allow the impact to be channelled in the desired direction, causing further damage.
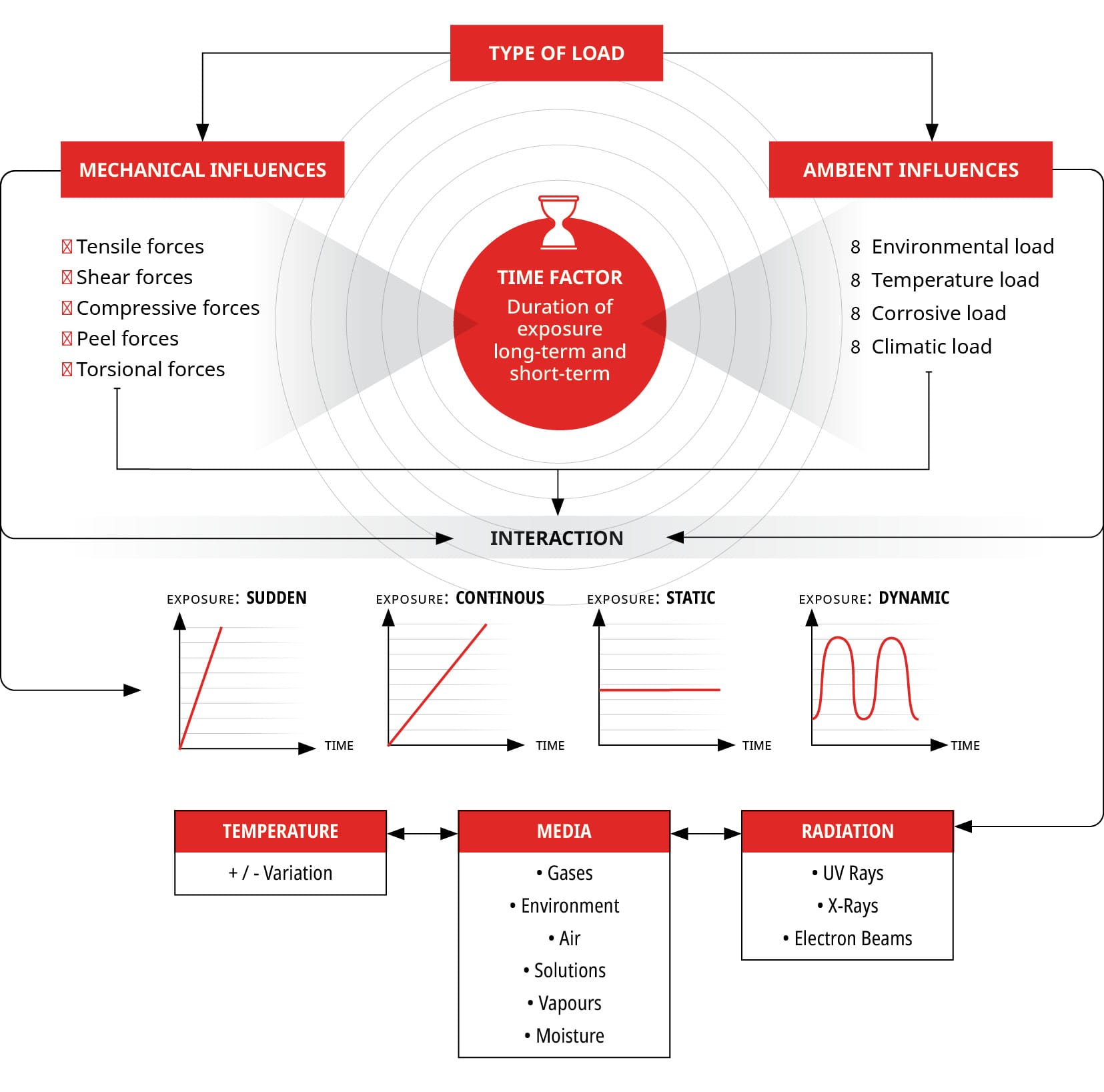