2.2.4 External Acting Forces
Another important consideration when selecting materials and joining methods is factors outside of the system and the design parameters for the finished components. Cyclic stresses, particularly slow ones, are much more damaging to materials and joined assemblies than steady stress. The materials and joining method(s) selected for a particular application must resist these loads and stresses, even after sustained exposure to environmental factors encountered during the life of the assembly. Externally acting forces and applied loads can lead to fatigue, deformation, weakening and degradation of parts and materials. These effects are amplified or highlighted if an unsuitable method of joining is selected, even more so if an inconsistent joining method combines with a questionable material selection, which has been known to occur in the manufacture of low-cost consumable items.
the main loadings of bonded joints
- Tensile and compressive stresses produced by out-of-plane tensile or compressive loads
- Shear stresses produced by tensile, torsional or pure shear loads imposed on substrates
- Cleavage loads produced by out-of-plane tensile loads acting on stiff and thick substrates at the ends of the joints
- Peel loads produced by out-of-plane loads acting on thin substrates.
These loads will also affect assemblies joined using other methods and processes; however, many traditional ways of joining materials will be subject to other forces that result from the load types. For example, a bolted or riveted assembly will have stress concentrations around the holes or areas of less material. Under loads exceeding the design capabilities, or in high-impact situations, such as crashes, failure of the material and joint will occur at the point(s) of highest stress, i.e. around the rivets or bolt holes. By comparison, a bonded joint will spread and accommodate continuous and shock loads more evenly.
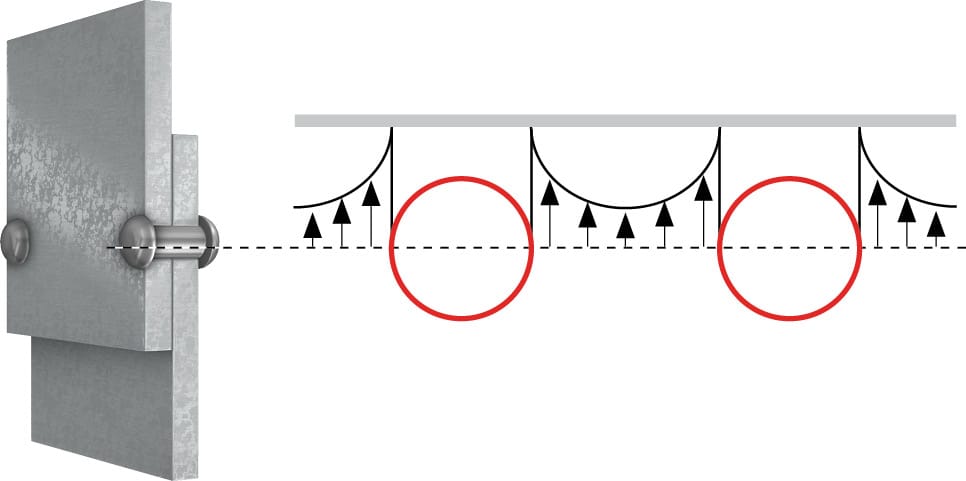
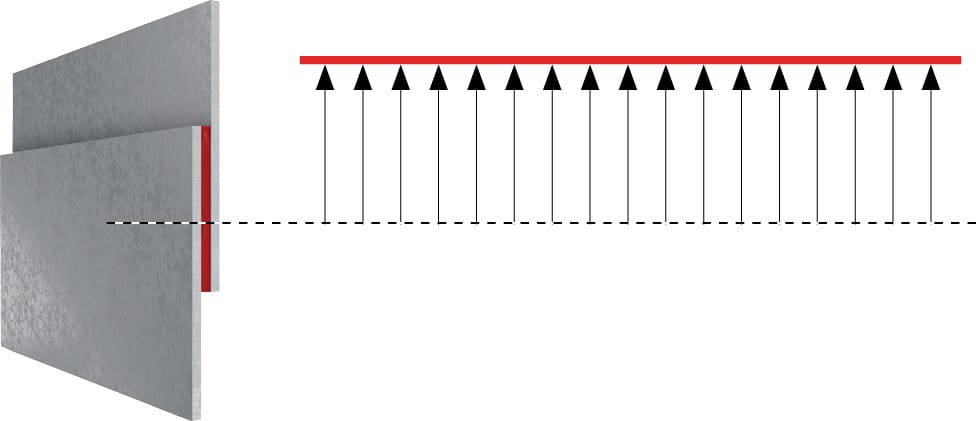
While later sections focus on joint design and common failure modes of materials and joined assemblies, this section discusses a few factors and loads that may affect a material and joining method. Beyond the environmental factors addressed and the expected loads that are foreseen in the early design phases of a product, there are several additional factors to consider:
- Pressure
- Vibration
- Variable loading through substrates or from peripheral features
- Impact and shock