2.2.3.4 Chemical Resistance
Another factor affecting substrate materials, joining methods and joint durability is solvent and chemical exposure. There are many materials, compounds and solutions that can chemically attack a material, leading to both visual and structural changes of the substrate and the chosen joining method.
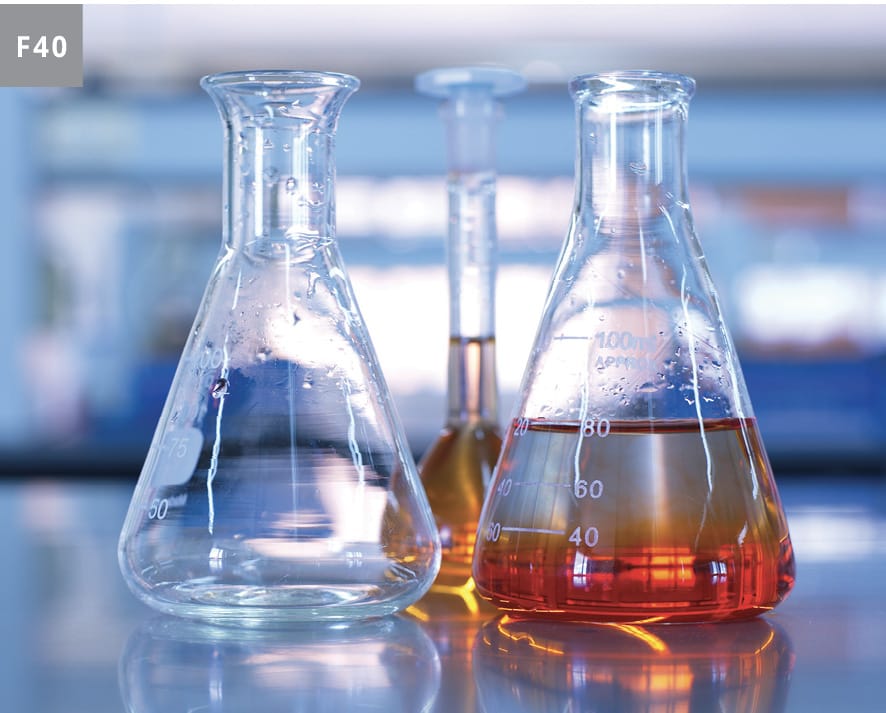
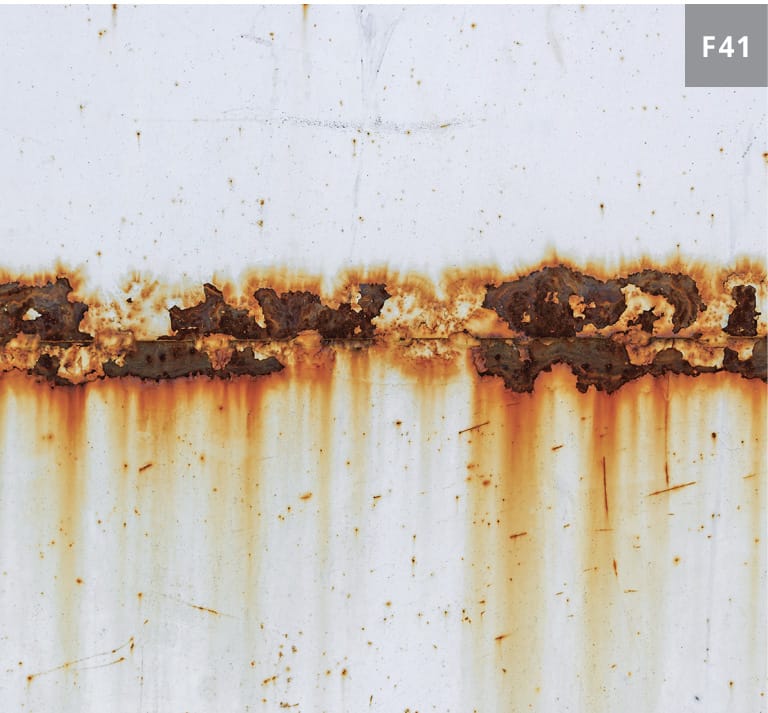
Corrosion is an attack on a material, most often metallic, that results from a chemical or electrochemical reaction with the surrounding media and environment.
Material damage and subsequent component failure due to corrosion can be eliminated by selecting the optimum material for a given application. The corrosiveness of a liquid on metals is mainly dependent on the liquid’s oxygen, chloride and/or sulphide content, temperature and pH. Chemical corrosion of a material can be combatted and counteracted at the design phase with the selection of appropriate materials, a suitable design for the product considering the operating environment, protective coatings, correct installation/maintenance and sufficient testing. Contact with corrosives can damage containers, equipment, installations and building components made from unsuitable materials. The stronger the corrosive and the higher the temperature, the greater the rate of metal corrosion. When acids attack metals, hydrogen gas is often given off. This is a flammable gas which can burn or explode if an ignition source is present. Common bases, such as sodium hydroxide and potassium hydroxide, can also attack metals like aluminium, zinc, galvanised metal and tin to produce hydrogen gas. It is important to review the relevant safety data sheet (SDS) for a particular corrosive and understand what metals or other materials, such as plastics or wood, it will attack.4
The resistance of polymers to corrosives is dependent on the structure of a given polymer. Some polymers, such as cellulose acetate, do not exhibit outstanding resistance to acids and alkalis. Most polymers are less brittle than more chemically resistant ceramics and are more resistant to corrosives than most metals. The rate of attack of polymer molecules by corrosives may be enhanced or hindered by the presence of neighbouring groups. Carbon-to-carbon bonds are not readily cleaved by acids, bases and corrosive materials, whereas carbon bonds with oxygen, sulphur or nitrogen, which are ionic and/or highly polar in nature,.5 are more readily cleaved.
4) Canadian Centre for Occupational Health and Safety, 2008, Corrosive Materials – Hazards, 6th May 2021.
5) R. B. Seymour et al., Structure – Property Relationships in Polymers (New York: Plenum Press, 1984).
In a chemical attack, a reaction takes place on the molecular chain of the polymer or elastomer. Often such reactions will cause the chain to break or ‘unzip’. When a plastic/elastomeric part experiences a chemical attack, the smaller segments of the molecular chain will have reduced entanglement; this lowers the material’s tensile strength, tensile elongation and impact resistance, leading to a failure of the manufactured components.
Physical absorption does not involve a chemical reaction with the polymer chain; instead, the chemical is absorbed into the plastic, much like how water is absorbed into a sponge. Once inside, the chemical can cause changes in the weight, hardness and dimensions of a plastic part. In some cases, the chemical acts as a plasticiser, making the plastic softer and more flexible. In other cases, the chemical extracts a plasticiser that was part of the original formulation, causing the plastic or elastomer to become brittle.6
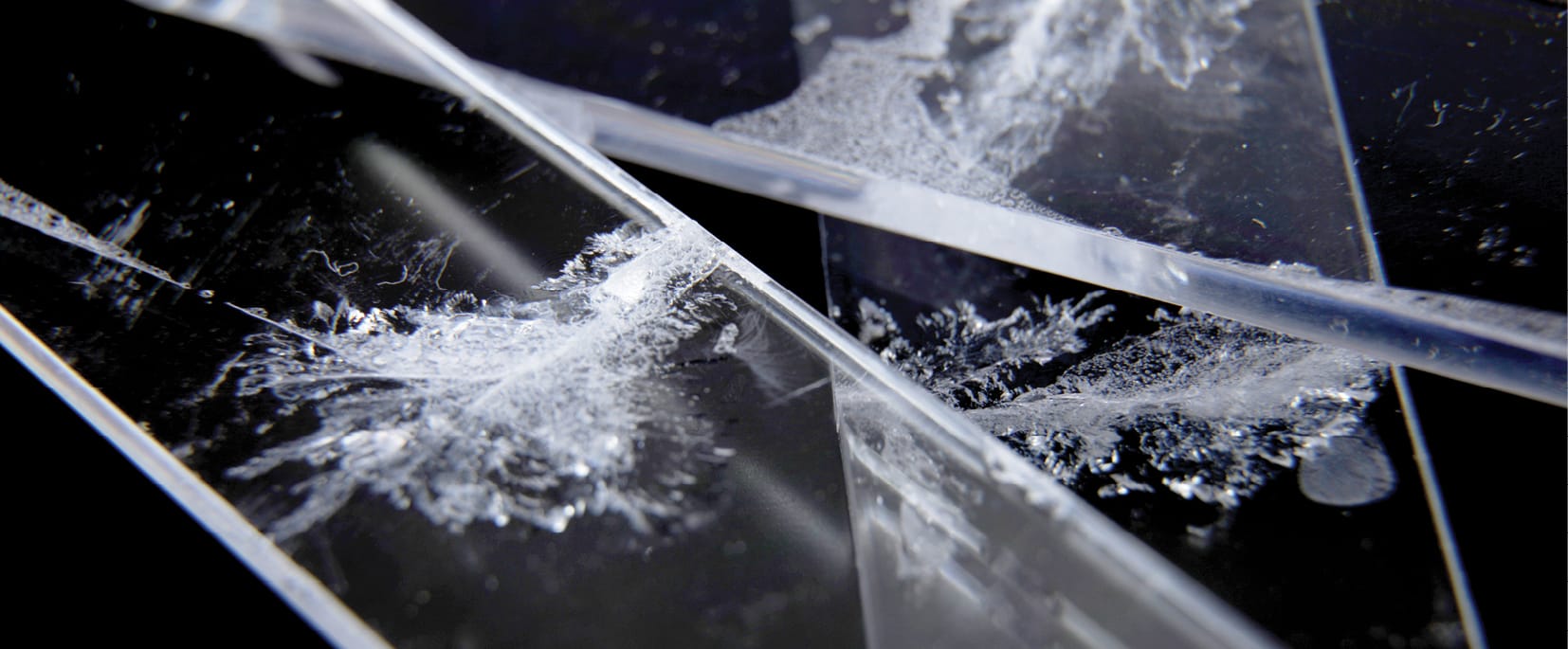
The presence of internal and external stresses makes plastic parts more vulnerable to chemically induced failures. Internal stresses are introduced into a part during processing and fabrication. External stresses are the result of the mechanical loads applied to a plastic part. Environmental stress-cracking occurs when a chemical sufficiently weakens the plastic to allow internal and external stresses to initiate localised cracking, known as crazing.
Assessing the expected longevity of a plastic or elastomeric part requires knowing the manner of exposure to a chemical. Chemical reactions sometimes require considerable time before appreciable damage takes place. Wiping away incidental splashes, where possible, before they can be absorbed into the plastic can help extend the lifetime of a component. The more surface area that is exposed to a chemical, the likelier it will undergo a chemical attack.
Creating designs that limit the surface area exposed to chemicals can also help extend part life and reduce failures or unexpected downtime.
6) Curbell Plastics, Selecting Plastic Materials for Use in Chemical Environments, 6th May 2021.
Typically, glass is considered a chemically resistant material. Glass is resistant to most acids but is highly susceptible to attack by alkaline materials. For applications that require operation in conditions where strong bases are expected, specialist grades of glass, such as borosilicate, should be specified.
The use of wood in chemical processing and for the storage of corrosive chemicals is well established, and wood is generally regarded to possess a high degree of resistance to degradation by numerous chemicals. Wood is most severely attacked by strong acidic and caustic solutions, representing extremes in pH values, and by powerful oxidising agents.7 Different woods vary greatly in their resistance to chemical degradation, but overall, softwoods display more resistance than hardwoods.
Given the wide range of behaviours of common engineering materials when in contact with solvents/chemicals, it is critical to fully understand a material’s capabilities and to know the range of environments and media to which a finished component may be exposed. Components and designs are expected to operate in numerous harsh environments, ranging from direct contact with fuels and lubricants to operating near radioactive substances and immersion in plant water and wastewater. Consideration must be given to the performance and changes in both the selected materials and the proposed joining method. A selected joining method will require a material (e.g. steel bolts or an epoxy adhesive) that performs the function of joining, securing or sealing a given number of surfaces, is resistant to the expected media and can withstand the loads and forces applied to it during operation.
7) A. Kass, F. Wangaard and H. A. Schroeder. Chemical Degradation of Wood: The Relationship Between Strength Retention and Pentosan Content, Wood and Fiber Science, Issue Number 1 / Spring 1970.
SUBSTRATES | WATER | ALCOHOLS | FUELS | Oils/ Lubricants | ACIDS | ALKALIS | |
METAL | (Anodised) Aluminium | ||||||
(Stainless) Steel | |||||||
PLASTIC | Standard Plastic | ||||||
Engineering Plastic | |||||||
High Performance Plastic | |||||||
Rubber | |||||||
Composites | |||||||
Glass | |||||||
Hardwood and Softwood | |||||||