2.2.3.3 External Environment and Humidity
Figure 37 External weather conditions
When designing parts and components for external use, it is important to consider environmental factors other than temperature. Humidity and moisture can have a detrimental effect on many materials and joining methods. Vehicles produced in the automotive industry several decades ago were plagued by rust and corrosion issues in seams and body panels, as well as rivets and other mechanical joining methods. Beyond basic consideration of the substrate materials and the most suitable method of joining, protective coatings, paints and finishes can be applied to increase the durability and longevity of the components. Overall, the critical performance factors driving the development and use of coating technologies to protect exposed surfaces are (a) aesthetic characteristics, (b) corrosion protection, (c) mass production, (d) cost and environmental requirements and (e) appearance and durability.3 Although the relative importance of each of these factors is debatable, the perfection of any one at the expense of another could be unacceptable and uncover hidden flaws in the design or material selection. These are key points to note, particularly when selecting metals that are not known for long-term resistance to moisture and humidity, such as iron or steel, or when such materials are not pre-treated to achieve the necessary long-term performance, i.e. raw aluminium is known to corrode, while anodised finishes will offer longer lifespans without showing signs of degradation.
3) Nelson K. Akafuah, Sadegh Poozesh, Ahmad Salaimeh, Gabriela Patrick, Kevin Lawler, and Kozo Saito, Evolution of the Automotive Body Coating Process—A Review. Mechanical Engineering Faculty Publications. 25. 2016.

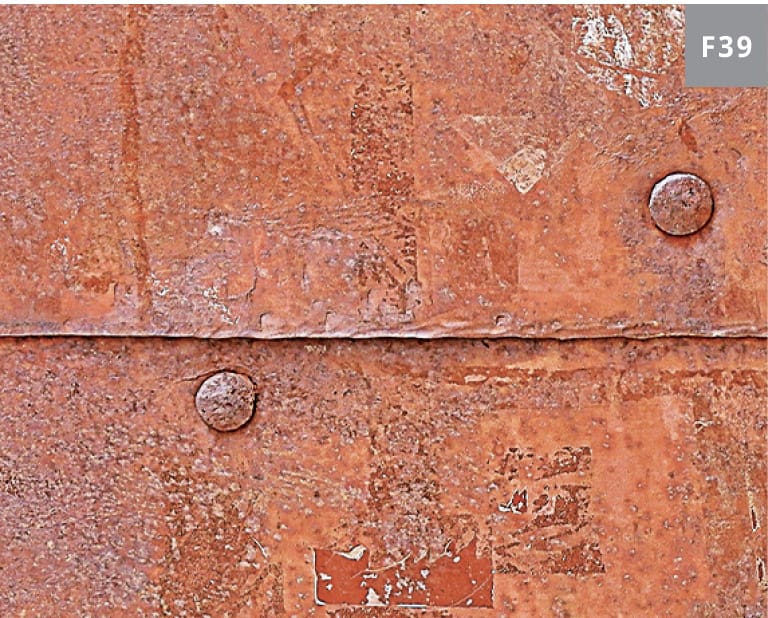
Many engineering plastics are inherently resistant to moisture and humidity, with thermoset polymers often being selected over cheaper thermoplastics when high performance is required. Each application is different and, often, operating conditions and performance requirements must be balanced or prioritised to ensure that parts offer the desired or necessary features, even after extended ageing.
Moisture and humidity may not affect or degrade the chosen materials, but the behaviour of the materials when exposed to moisture needs to be observed – glass is permeable and will allow the transmission of moisture, whereas woods may swell and soften as they absorb water. All of these differing behaviour traits and characteristics of materials will impact the choice of joining method. Rivets and bolts may be used to fix non-permeable or moisture-resistant surfaces, but these fasteners in turn may be subject to attack by moisture, rendering the choice of exposed surface materials moot.
In addition to noting the hygroscopic or hydrophobic nature of materials and fasteners when exposed over their life cycles, relative humidity will also affect production and assembly processes. High relative humidity can cause condensation to form on surfaces, leading to flash rust/corrosion of some metals and reduced friction on parts where mechanical interference is required for fixing or securing mating surfaces. Regardless of the proposed or specified joining method, overall success demands an understanding of how environmental factors will impact the chosen materials and fasteners in the long-term, as well as during production.