2.2.3.2 Temperature Changes and Thermal Cycling
Temperature changes can have a significant impact on materials and the selected joining method. Consideration must be given to the average operating temperature as well as the potential range of temperatures the assembly may be exposed to during its lifetime.
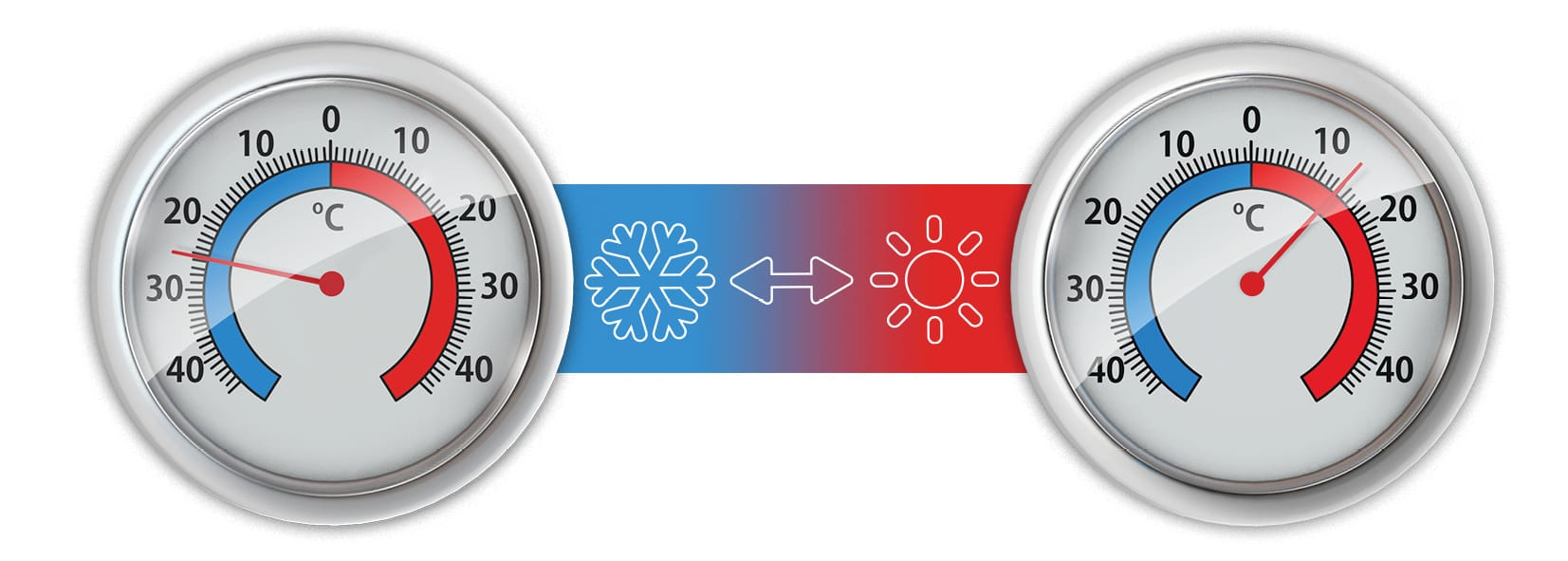
Significant impacts of elevated temperatures are the expansion, softening and relaxation of materials. When designing components, it is critical to observe the capabilities and known resistance of the substrates. For example, heating systems commonly use metallic components because of their ability to withstand high operating temperatures while offering the necessary mechanical performance. Applications that combine the need for rigidity, high strength and high temperature resistance typically limit the use of polymers, rubbers, wood and glass. Understanding how a material will perform under specific or expected conditions is vital.
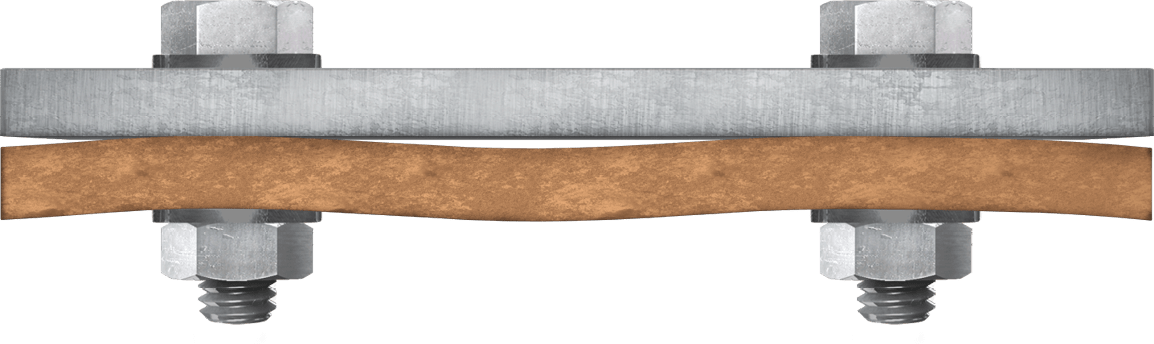
SUBSTANCE | Aluminium | Brass | Copper | Steel | Silver | Gold |
(K^-1) | 2.4 x 102 | 1.9 x 102 | 1.7 x 102 | 1.2 x 102v | 1.93 x 102 | 1.3 x 102 |
SUBSTANCE | Platinum | Tungsten | Glass (Pyrex) | Glass (Ordinary) | Concrete | |
(K^-1) | 8.6 x 102 | 0.4 x 102 | 0.4 x 102 | 0.9 x 102 | 1.2 x 102 |
In addition to the change in the physical properties of substrates at elevated temperatures, it is important to consider the expansion of materials and ensure that the maximum and minimum permissible change in dimensions is within the scope and capabilities of the intended application. Thermal expansion and contraction can have a greater impact and require further consideration when joining dissimilar materials. It is also important to check the differential of thermal expansion for each material and calculate the maximum dimensional change for each part to confirm the feasibility of the proposed material combination. Over time, repeated condition cycles that vary the dimensions and properties of a material can be translated into a permanent change. Metal parts, such as railway tracks, are constantly exposed to external environments and are subjected to repeated thermal cycles and variable conditions. Despite deliberate gaps being left between joint sections of the track to accommodate thermal expansion, they can creep dimensionally and become permanently distorted after repeated exposure to thermal cycles. This cyclic expansion and contraction can cause gaps and misalignments to become apparent and pose significant safety risks. Identifying how critical a part is and understanding the effects of failure play a big part in the selection of materials and subsequent joining methods.
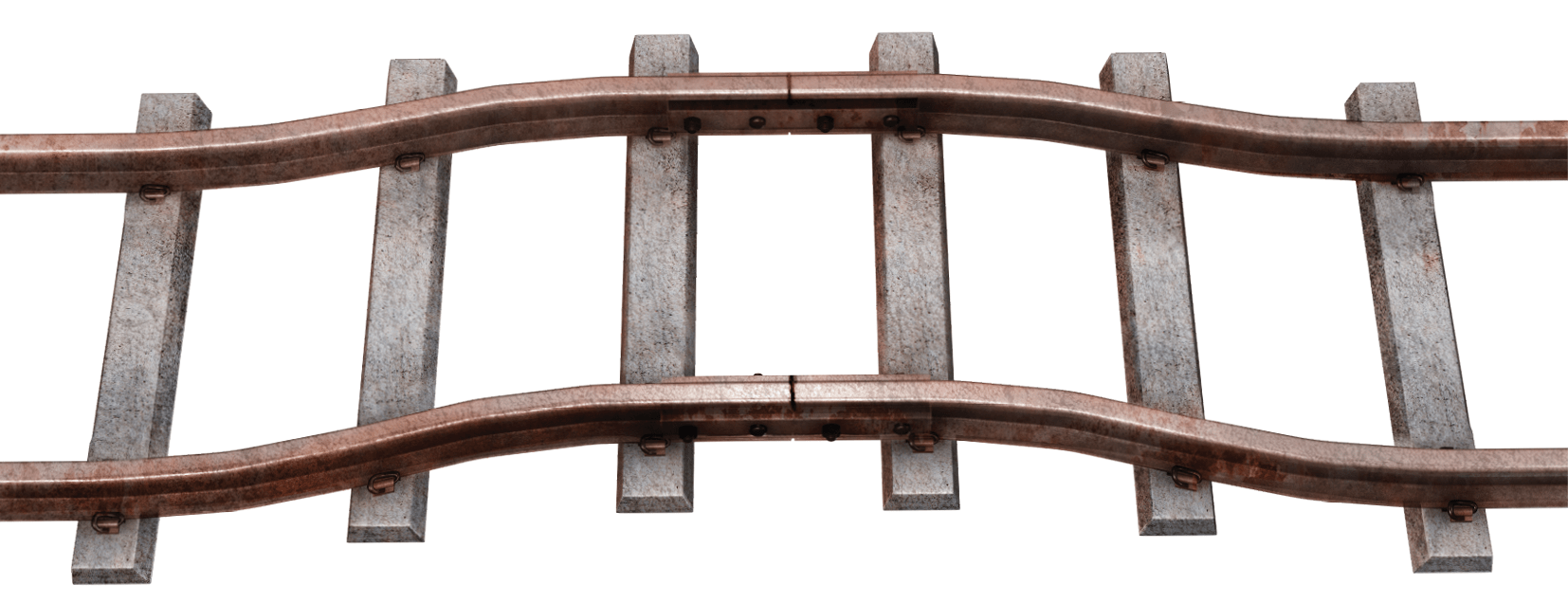
Externally acting forces and applied loads can lead to fatigue, deformation, weakening and degradation of parts and materials, which can be exacerbated or accelerated by extreme high or low heat. As previously noted, high heat can result in expansion, softening and relaxation, while low temperatures will cause materials to contract and shrink dimensionally. Low temperatures will also make substrates brittle and rigid – and harder is not always better. In the same way that applications calling for strong, rigid materials must be able to withstand the changes that occur at high temperatures, an application that requires flexible substrates, i.e. gasketing with rubber O-rings, must be able to accommodate the physical and dimensional changes that occur under low temperatures.