Section Two The Basics of Joining
Prior to selecting a particular joining method, many factors need to be understood to create the most reliable and effective assembly. Each assembly is different, the goal of this section is to establish an understanding of the processes used to identify appropriate substrates and to define important characteristics that impact joining method selection. Factors such as specific assembly strength requirements, testing requirements, applied forces and loading conditions, the permanence and required durability of an assembly, manufacturing and design parameters, and substrate characteristics need to be considered before selecting a joining method. It is also important to quantify these factors to ensure that the final assembly meets and, where possible, exceeds the minimum performance expectations. This section covers these topics in depth.
2.1 Introduction
Companies are under increasing pressure to meet consumers’ expectations for high quality products while operating more efficiently with less downtime. One of the major goals in manufacturing processes is to maximise overall equipment effectiveness (OEE), to reduce and/or eliminate what are known as the ‘Six Big Losses’ 2 – the most common causes of equipment-based productivity loss in manufacturing.
Overall Equipment Effectiveness | Updated | Traditional |
Availability Loss | Unplanned Stops Planned Stops | Equipment Failure Setup and Adjustments |
Performance Loss | Small Stops Slow Cycles | Idling and Minor Stops Reduced Speed |
Quality Loss | Production Rejects Startup Rejects | Process Defects Reduced Yield |
OEE | Fully Productive Time | Valuable Operating Time |
This OEE assessment involves not only equipment maintenance but all aspects of machine operation, installation and production. This approach can also be applied to operators and production staff. OEE measurement is based on the top three categories of six big losses: availability rate/loss, performance rate/loss and quality rate/loss. Although it is difficult to achieve zero loss, it is believed that striving for zero defects is an important prerequisite for the success of the total productive maintenance (TPM). Table 2 defines the ideal OEE values.
2) Six Big Losses, https://www.oee.com/oee-six-big-losses.html#equipmentFailure.
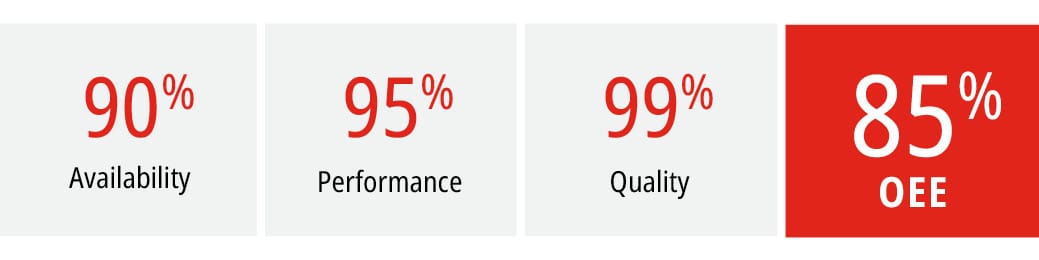
To achieve these optimum values, where 100% equates to perfect production, the process of product development must be meticulously considered. Section 2.2 describes the factors that can affect assembly quality. OEE should achieve a value of >85% by effectively reducing the impact of the six big losses. With OEE scores in this range, production will run as efficiently as possible. The quality of a finished product should be directly proportional to the manufacturing process; a higher OEE score translates to an improved final assembly. Constant quality control throughout the entire production cycle is necessary to deliver the highest quality product. Testing is one of the most efficient and valuable quality control tools used by manufacturers. Many joining methods can be used to maximise the effectiveness of a piece of equipment, assembly or joint; however, proving the effectiveness is critical.