1.1 Conventional Methods for Joining
Joining materials are mechanical, thermal and chemical. Mechanical joining relies on devices such as bolts and rivets, or on the distortion of the material itself, such as folding, press-fitting or shrink-fitting, to secure the components of an assembly. Thermal joining methods for metals include welding, brazing and soldering. There are several thermal methods of plastic welding. Chemical joining methods include adhesive and, for plastics, solvent bonding. Every technique has pros and cons: operation conditions, expense, geometric tolerances and disassembly requirements are just some of the considerations when joining materials together.
1.1.1 Mechanical Joint: Threaded Fasteners
Threaded fasteners are the ideal method of mechanically joining elements when occasional and easy disassembly of the joined parts is required. Threaded fasteners require the expense of drilling and tapping the parts to be joined, often to specified tolerances. The fastener sites concentrate stress, which, if severe enough, may require the parts to be reinforced at those points. Threaded fasteners can provide a very strong clamping force but may fail over time due to vibration and cyclic loading, and corrosion is a concern in humid, marine or chemical environments. Adding a chemical bonding agent – an adhesive – to a threaded fastener can reduce or eliminate many of these issues. For an in-depth discussion of threadlocker adhesives and threaded assemblies in general, refer to the manual in this series titled How to Increase Reliability and Prevent Threaded Assembly Failure.
Figure 4 Stress risers occur at threaded fastener or rivet locations
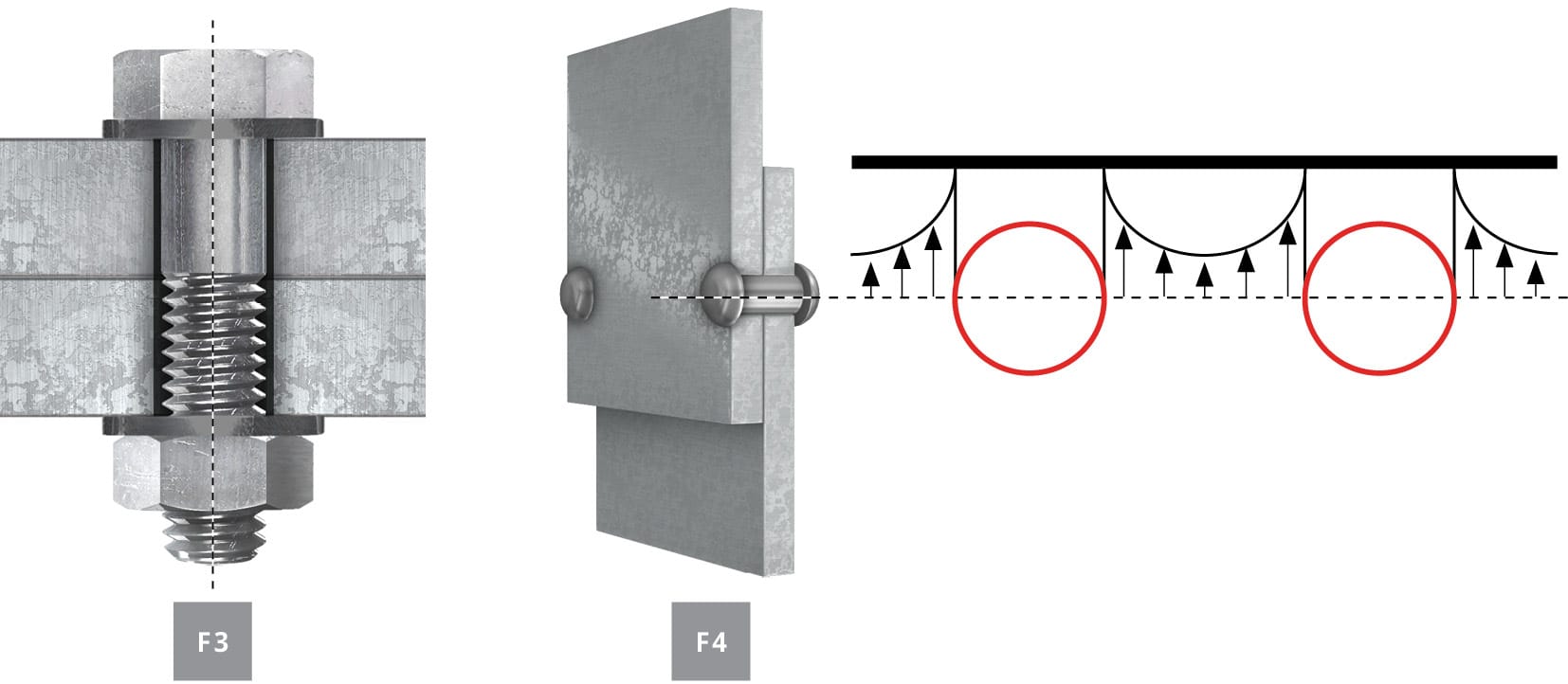